Production d'acier

La production d'acier ou fabrication de l'acier est l'ensemble des étapes nécessaires à l'élaboration de lingots, blooms, brames ou billettes ayant la composition finale de l'acier désiré. Elle se décompose en plusieurs grandes étapes : la métallurgie primaire (qui fournit l'acier en fusion), la métallurgie secondaire (où la composition du métal en fusion est ajustée), puis la coulée et sa transformation (par exemple, par laminage). C'est un sous-secteur d'activité, au sein du secteur d'activité de la métallurgie qui regroupe les activités de production de l'acier.
Lors de la première phase, la fabrication commence à partir du minerai de fer ou de la ferraille (chutes de métal). Lorsque le minerai de fer est utilisé, il peut être introduit sous forme d'aggloméré ou de boulettes dans un haut-fourneau pour être réduit grâce au coke, et produire de la fonte liquide. Il doit alors passer dans un convertisseur pour produire l'acier en fusion. Cette filière est la plus répandue. Alternativement, le procédé de réduction directe permet de transformer le minerai de fer sans passer par un haut-fourneau ou un convertisseur. Les fours à arc électrique sont alors utilisés pour produire l'acier en fusion à partir du minerai de fer préréduit ou de la ferraille.
Lors de la phase suivante, la métallurgie en poche a pour but de nettoyer l'acier (calmage, dégazage, affinage) et de le mettre à nuance (ajout des éléments d'alliage).
L'acier est ensuite coulé au travers d'une lingotière de section adaptée à la forme du demi-produit à fabriquer, en utilisant un procédé de coulée continue ou en lingots, puis est laminé aux dimensions souhaitées des brames ou des blooms.
L'acier[modifier | modifier le code]
L'acier est la matière fabriquée à partir de minerai de fer et de minerai de charbon. Sa fabrication en grande quantité requiert la maîtrise à la fois de réactions chimiques complexes et de très grandes unités de production.
Il faudra attendre le XIXe siècle pour que l'acier, alors fabriqué en faible quantité connaisse un développement spectaculaire et s'impose comme le métal-roi de la révolution industrielle.
L'acier a de nombreuses applications dans l'industrie. Il est utilisé dans la construction navale, la construction automobile, le bâtiment, l'emballage et bien d'autres secteurs.
L'acier est facilement récupérable au milieu d'autres déchets au moyen d'un tri magnétique. Son caractère magnétique lui permet en effet d'être attiré par un aimant. L'acier est recyclable à l'infini. Le recyclage permet de faire des économies de minerai, de chaux et d'énergie. La part de production d’acier issue du recyclage de ferrailles avoisine, selon les années, 40 % de la production mondiale d’acier.
Les ferrailles recyclées constituent jusqu'à 20 % de l'origine du fer élaboré par les procédés modernes en filière fonte. En effet, la ferraille sert d'agent refroidissant dans un convertisseur à oxygène.
Histoire[modifier | modifier le code]
Évolution de la fabrication d'acier pendant le XXe siècle[modifier | modifier le code]

Sources :
*International Iron & Steel Institut (http://www.worldsteel.org/) * Jacques Astier, Sidérurgie, Techniques de l'ingénieur, Matériaux métalliques page M7000, juin 2001
Définition :
Acier brut : acier liquide ou acier sous forme de demi-produit (brame, billette ou blooms). Il ne s'agit pas de produits finis (tôle, fil...).

Techniques[modifier | modifier le code]
Métallurgie primaire[modifier | modifier le code]
Usine d'agglomération[modifier | modifier le code]
Le minerai de fer possède des propriétés chimiques et physiques qui le rendent inexploitable en l'état par le haut fourneau. Il lui manque en particulier :
- la résistance mécanique nécessaire pour supporter l'écrasement dû à l'empilage des matières dans le haut fourneau ;
- la porosité permettant la circulation du vent des tuyères vers le gueulard ;
- la composition chimique en oxydes, pour maîtriser le laitier.
Les minerais sont préparés par broyage et calibrage en grains qui s'agglomèrent entre eux. Le mélange obtenu est cuit sous une hotte à 1 300 °C. L’aggloméré obtenu est ensuite concassé et calibré puis chargé dans le haut fourneau avec du coke.
Cokerie[modifier | modifier le code]
De façon simplifiée, le coke est du carbone presque pur doté d'une structure poreuse et résistante à l'écrasement. Il est utilisé comme un puissant réducteur. Il est obtenu à partir de la houille, après que celle-ci ait été libérée de ses composants indésirables. Pour cela on la fait cuire, à l'abri de l'air, dans les fours de la cokerie à 1 250 °C durant 17 heures. En brûlant dans le haut fourneau, le coke apporte la chaleur nécessaire à la fusion du minerai ainsi que le carbone nécessaire à sa réduction.
Haut fourneau[modifier | modifier le code]
On y extrait le fer de son minerai. Minerai et coke solides sont enfournés par le haut, le gueulard. L'air chaud (1 200 °C) insufflé à la base provoque la combustion du coke (carbone presque pur). Le monoxyde de carbone ainsi formé va réduire les oxydes de fer, c'est-à-dire leur prendre leur oxygène et, de ce fait, isoler le fer. Il se chargera cependant en carbone pendant son séjour dans le creuset et se transformera en fonte. La gangue est un produit secondaire du haut fourneau (c'est la part stérile du minerai de fer) ; elle est récupérée, à la sortie du haut fourneau, à l'état liquide, mêlée à d'autres oxydes. La densité moindre de ce résidu le fait flotter au-dessus de la fonte. Ce résidu est appelé laitier de haut fourneau et est principalement exploité pour la fabrication du ciment.
Convertisseur à l'oxygène =[modifier | modifier le code]
Cet outil assure la conversion de la fonte en acier.
La fonte en fusion est versée sur un lit de ferrailles. On brûle les éléments indésirables (carbone et résidus) contenus dans la fonte en insufflant de l'oxygène pur. Il s'y forme, là aussi, un résidu, le laitier d'aciérie, qui est séparé de l'acier au moment de la vidange du convertisseur. On obtient de l'acier liquide sauvage, qui est versé dans une poche. Il est appelé acier sauvage, car, à ce stade, s'il était coulé, il se solidifierait en provoquant de nombreuses projections dues au rejet des gaz dissous (essentiellement du monoxyde de carbone).
Réduction directe[modifier | modifier le code]
La réduction directe est un ensemble de procédés d'obtention de fer à partir de minerai de fer, par réduction des oxydes de fer sans fusion du métal. Le produit obtenu est du minerai de fer préréduit.
Historiquement, la réduction directe concerne l'obtention d'une loupe au bas fourneau. Ce procédé a été abandonné, au début du XXe siècle, au profit du haut fourneau qui produit du fer en deux étapes (par réduction-fusion donnant une fonte, puis par affinage dans un convertisseur).
Mais divers procédés ont été mis au point au cours du XXe siècle et, depuis les années 1970, l'obtention de minerai de fer préréduit a connu un développement industriel remarquable avec l'essor, notamment, du procédé Midrex. Conçus pour remplacer le haut fourneau, ces procédés ne se sont jusqu'ici avérés rentables que dans certains contextes économiques particuliers, ce qui limite encore cette filière à moins de 5 % de la production mondiale d'acier.
Four à arc électrique[modifier | modifier le code]

Un four à arc électrique est un type de four qui utilise l'énergie thermique de l'arc électrique, établi entre une ou plusieurs électrodes de carbone et le métal, pour obtenir une température suffisante à sa fusion. Il a été progressivement mis au point à partir de la fin du XIXe siècle. Sa capacité va généralement d'environ 1 tonne à 400 tonnes. Il est principalement utilisé pour la production d'acier liquide (environ 35 % de la production mondiale).
Métallurgie en poche[modifier | modifier le code]
Le rôle de la métallurgie en poche consiste à mettre à nuance et à température l'acier liquide issu du convertisseur.
Mise à nuance[modifier | modifier le code]
Elle comporte plusieurs étapes, toutes facultatives, et dont l'ordre peut changer :
- le calmage de l'acier sauvage qui va consommer l'oxygène dissous dans l'acier. Pour cela, on jette dans l'acier liquide de l'aluminium (pour les produits plats) ou du silicium (cas des produits longs) qui, en s'oxydant, vont transformer l'oxygène dissous en oxydes ;
- le dégazage : l'acier va passer par un passage sous vide destiné à parfaire la décarburation entamée au convertisseur (dans ce cas-ci, il est nécessaire de conserver, au préalable, un minimum d'oxygène dissous). A cette étape on peut retrouver les opérations de déshydrogénation et, parfois, de dénitruration (abaissement de la teneur en hydrogène et azote respectivement) ;
- l'ajustement du laitier de poche, de manière qu'il ait la capacité d'absorber les impuretés comme les oxydes produits par le calmage ;
- l'affinage qui va ôter les derniers éléments indésirables, comme le soufre (désulfuration) ;
- l'ajout des éléments d'alliages.
Mise à température[modifier | modifier le code]
La coulée continue demande typiquement des températures d'acier d'environ 30 °C au-dessus du liquidus de l'alliage. Les moyens de réchauffage sont, soit le four électrique à poches, soit un procédé chimique comme l'aluminothermie. Il est également possible de travailler tout le temps très chaud, pour ne refroidir à la bonne température qu'au dernier moment.
Coulée[modifier | modifier le code]
Coulée continue[modifier | modifier le code]
L'acier liquide est coulé, à environ 1 560 °C, dans une lingotière en cuivre de section carrée, rectangulaire ou ronde (selon le demi-produit fabriqué).
Au contact des parois de la lingotière, le métal se solidifie instantanément et commence à former une peau solide. L'acier est ensuite tiré vers le bas par un jeu de rouleaux et d'extracteurs et il achève de se solidifier, grâce essentiellement à des jets d'eau pariétaux.
À cause du refroidissement intense, le métal subit une histoire thermomécanique, lors de son parcours dans la machine de coulée continue. En fonction de cet historique (influencé notamment par la vitesse de coulée, la forme de la machine, l'intensité du refroidissement), la qualité du produit est plus ou moins bonne et le sidérurgiste pourra vendre plus ou moins cher le produit.
La coulée en lingots[modifier | modifier le code]
La coulée peut être également faite en lingotière. Ce procédé, peu performant en termes de mise au mille permet cependant l'obtention d'alliages spécifiques, comme les aciers non calmés.
L’acier est coulé et solidifié dans des moules en fonte : les lingotières.
Une fois la solidification terminée, les lingots sont démoulés (le « strippage » (de l'anglais to strip qui signifie « retirer »).
Transformation[modifier | modifier le code]
Après un réchauffage à 1 200 °C, les produits coulés sont écrasés dans un gros laminoir pour être transformés en brames (étape de « slabbing », pour les produits plats) ou en blooms (étape de « blooming », pour les produits longs).
Répartition géographique[modifier | modifier le code]
Les chiffres de consommation sur dix ans montrent une très forte augmentation de la demande d'acier par la Chine. En 2004, la demande chinoise entraîne des fortes augmentations de prix de l'acier (de 20 à 50 %). Elle crée également des tensions pour l'approvisionnement. Un fait symptomatique, le fabricant automobile japonais Nissan a fermé pendant une semaine (du au ) trois usines sur les quatre qu'il possède au Japon à cause de rupture d'approvisionnement en acier (et probablement d'une politique d'achat trop agressive). Ces fermetures ont entraîné un déficit de fabrication de vingt-cinq mille voitures soit une perte de quarante-quatre millions d'euros.
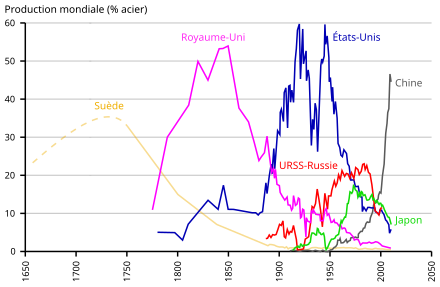
Production en fonction du développement économique[modifier | modifier le code]
La production d'acier n'est strictement proportionnelle au Produit intérieur brut qu'en période d'industrialisation. Comme beaucoup de commodités (ciment, papier, etc.), les besoins, donc la production, décroissent généralement lorsque la croissance est tirée par des techniques de pointe, les services, etc.[2].

Pour la plupart des pays, la production d'acier s'infléchit après avoir atteint un PIB donné, signe que la croissance se poursuit sur d'autres principes.
Acteurs[modifier | modifier le code]
Les principaux producteurs au monde sont les entreprises suivantes : Arcelor-Mittal, JFE Holdings, Nippon Steel, POSCO, Corus, ThyssenKrupp AG, Baosteel, Riva, Sumitomo, Erasteel.
Production mondiale[modifier | modifier le code]
La production mondiale recule de 0,9% en 2020, à 1,86 milliard de tonnes.
Pays | Production, 2019 (en millions de tonnes) | |||
---|---|---|---|---|
1 | ![]() |
996,3 | ||
2 | ![]() |
111,2 | ||
3 | ![]() |
99,3 | ||
4 | ![]() |
87,9 | ||
5 | ![]() |
71,6 | ||
6 | ![]() |
71,4 | ||
7 | ![]() |
39,7 | ||
8 | ![]() |
33,7 | ||
9 | ![]() |
32,2 | ||
10 | ![]() |
31,9 | ||
11 | ![]() |
23,2 | ||
12 | ![]() |
22,1 | ||
13 | ![]() |
20,8 | ||
14 | ![]() |
20,1 | ||
15 | ![]() |
18,6 | ||
16 | ![]() |
14,5 | ||
17 | ![]() |
13,6 | ||
18 | ![]() |
12,8 | ||
19 | ![]() |
9,1 | ||
20 | ![]() |
9,0 | ||
Source : WorldSteel 1WorldSteel 2 |
Impact environnemental[modifier | modifier le code]
La sidérurgie est une industrie à fort impact sur le climat : en 2021, elle concentre à elle seule 7 % des émissions mondiales de gaz à effet de serre et 11 % des émissions de CO2, soit 2,6 milliards de tonnes de CO2 par an[3],[4],[5],[6].
En raison des températures élevées à atteindre durant la fabrication et des émissions inhérentes au procédé, la décarbonation de la sidérurgie est plus difficile que celle du secteur de l'énergie[3]. Elle est pourtant nécessaire pour atteindre la neutralité carbone[3]. En 2020, l'industrie est en retard sur le scénario de neutralité carbone de l'agence internationale de l'énergie, l'intensité des émissions de la sidérurgie (par tonne d'acier produite) n'ayant que faiblement baissé depuis 2010[7]. Au début de la décennie 2020, les perspectives prévoient une poursuite de l'augmentation des émissions du secteur, en raison du cadre législatif en vigueur et du rythme de l'industrie : les volumes de production augmentent plus vite que les gains d'efficacité[4].
Produire une tonne d'acier par le procédé de fabrication basé sur l'utilisation du charbon dans un haut fourneau émet entre 1,8 et 2,2 tonnes de CO2[6],[8]. Cette méthode traditionnelle est aujourd'hui utilisée pour produire 70 % de l'acier mondial. Afin de réduire ces émissions, les industriels ont déjà travaillé sur l'optimisation de leurs hauts fourneaux, via l'ajout de ferrailles recyclées ou la réutilisation des gaz et de la chaleur induits. La production d'acier à partir de ferrailles récupérées, dans des fours électriques, assure déjà 20 % de la production mondiale d'acier et même 40 % en Europe. Les fours électriques n'émettent plus que 300 à 700 kg de CO2 par tonne d'acier, en fonction de l'origine de l'électricité utilisée. Le procédé de fabrication de l'acier par four à arc électrique (production secondaire, à partir de rebuts) est significativement plus économe en énergie et en GES que celui par haut-fourneau (production primaire, à partir du minerai de fer)[4],[7]. La principale contrainte à l'utilisation du four à arc électrique est la disponibilité de la ferraille[7].
En 2022, les pays ayant les émissions intensives de CO2 les plus faibles sont l'Italie, les États-Unis et la Turquie en partie grâce à une forte proportion de fours à arc électrique, tandis que l'Ukraine, l'Inde et la Chine occupent la fin du classement à cause de l'utilisation plus élevée de hauts-fourneaux[4].
Dès le début de la décennie 2020, l'agence internationale de l'énergie constate que — bien que nécessaires — les actions d'efficacité énergétique et d'amélioration de la collecte des produits en fin de vie ont une portée insuffisante[7]. Pour atteindre des réductions d'émissions plus importantes, de nouvelles technologies devront être mises en place : production à partir d'électricité décarbonnée, utilisation d'« hydrogène vert », captage du carbone, etc.[7] Les efforts des sidérurgistes pour aller plus loin se concentrent sur l'opération de réduction du minerai de fer, c'est-à-dire d'extraction de l'oxygène pour obtenir du fer quasiment pur. Certains aciéristes opèrent déjà de telles « réductions directes » à l'aide de gaz naturel. L'objectif à terme est de remplacer le gaz naturel par de l'hydrogène vert, produit par électrolyse grâce à de l'électricité décarbonée.
En 2022, trois projets de nouvelles technologies sont particulièrement suivis : le projet Hybrit du suédois SSAB (remplacement du coke de charbon par de l'hydrogène), le projet d'ArcelorMittal en France « 3D Carbon Capture » (captage du carbone) et le procédé HIsarna[7]. D'autres projets sont en cours chez ArcelorMittal (en Europe), chez Thyssenkrupp (sur son site de Duisbourg), et Voestalpine (sur son site de Linz). Au total, l'association des sidérurgistes européens Eurofer a identifié 54 projets de décarbonation, qui permettraient de réduire les émissions d'un tiers en Europe durant la décennie 2020-2030, au prix d'une augmentation du coût de l'acier estimée dans une fourchette de +35 à +100 % à l'horizon 2050[9].
En septembre 2023, la start-up suédoise H2 Green Steel, créée en 2021, parvient à réunir 1,5 milliard € de fonds propres pour construire la première aciérie 100 % décarbonée à Boden, dans l'extrême nord de la Suède ; ces fonds propres lui permettent de sécuriser 3,5 milliards € de dettes, notamment auprès de Société Générale et BNP Paribas, afin de financer son investissement estimé à 5 milliards €. L'usine doit démarrer sa production fin 2025 avec un objectif de 2,5 Mt/an au départ, puis 5 Mt/an en 2030, en utilisant la technologie de la réduction directe du minerai de fer par de l'hydrogène vert, produit par électrolyse de l'eau grâce à l'hydroélectricité locale. L'éponge de fer quasiment pure obtenue grâce à la réduction directe sera fondue dans un four électrique pour obtenir de l'acier. L'aciérie consommera 10 TWh/an et bénéficiera du coût très compétitif de l'hydroélectricité disponible dans le nord de la Suède (entre 25 et 35 euros/MWh). H2 Green Steel a déjà signé de nombreux contrats de cinq ou sept ans avec de futurs clients, surtout dans l'automobile (BMW, Mercedes, Scania, ...), représentant 50 % de sa production future[10].
Voir aussi[modifier | modifier le code]
Notes et références[modifier | modifier le code]
- Françoise Berger, La France, l’Allemagne et l’acier (1932-1952) : De la stratégie des cartels à l’élaboration de la CECA, Université Paris-1 Panthéon-Sorbonne, , 1257 p. (lire en ligne), p. 316
- (en) Ivan Roberts, Trent Saunders, Natasha Cassidy et Gareth Spence, « China's Evolving Demand for Commodities », Reserve Bank of Australia,
- Faustine Delasalle, « This is how the steel industry is forging a path to net-zero », sur weforum.org, (consulté le )
- Ali Hasanbeigi, « Steel Climate Impact », sur globalefficiencyintel.com, (consulté le )
- Comment décarboner la production de ciment et d’acier, Pour la Science, 2 mai 2022.
- « Recyclage, CCUS, hydrogène... Sept voies pour décarboner la production d'acier », Usine nouvelle, (lire en ligne)
- « Iron and Steel - Tracking report », sur iea.org, (consulté le )
- Kevin De Ras, Ruben Van de Vijver, Vladimir V Galvita et Guy B Marin, « Carbon capture and utilization in the steel industry: challenges and opportunities for chemical engineering », Current Opinion in Chemical Engineering, vol. 26, , p. 81–87 (ISSN 2211-3398, DOI 10.1016/j.coche.2019.09.001, lire en ligne, consulté le )
- « Acier vert » : le défi du siècle de la sidérurgie, Les Échos, 11 octobre 2021.
- H2 Green Steel va construire la première aciérie (verte) en Europe depuis 50 ans, Les Échos, 15 septembre 2023.
Articles connexes[modifier | modifier le code]
Liens externes[modifier | modifier le code]